The Art of Stamping Process Optimisation:
Delivering Consistent Quality
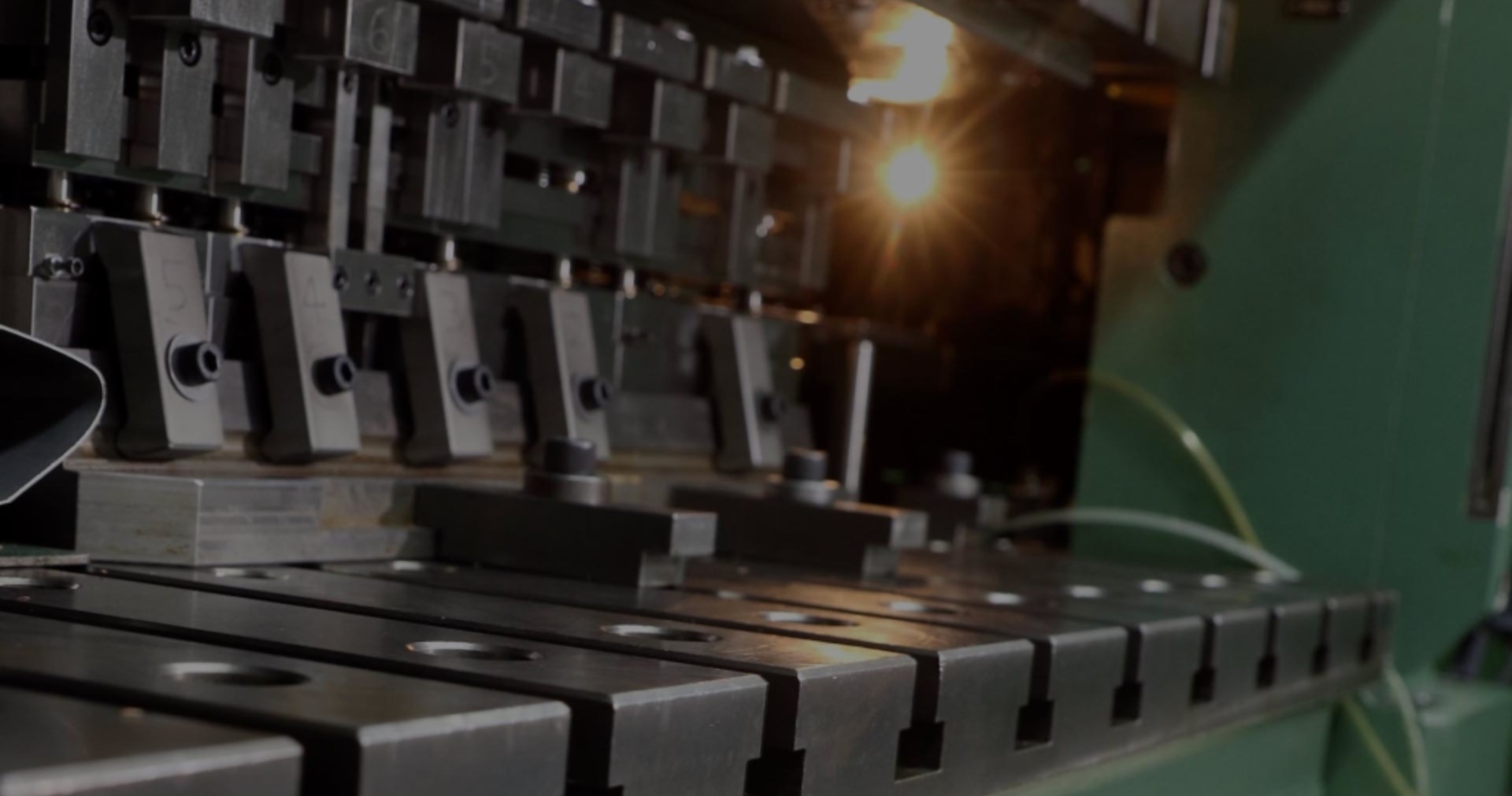
Introduction
Stamping is a fundamental process in manufacturing. The top-quality product is a testament to the company's commitment to delivering consistently high quality. By looking at our own approach, we’ll see how precision, efficiency, and innovation combine in the stamping process.
Table of Contents
The Stamping Process:
What is It?
Stamping, often regarded as a mainstay of modern manufacturing, is a process that transforms flat metal sheets into specific shapes through the application of high pressure.
This process can be categorised into various types, including punching, blanking, embossing, bending, flanging, and coining. Each method has a unique purpose and is chosen based on customer requirements.
The versatility of stamping allows for its application in various industries, from automotive to electronics, making it essential in the manufacturing world.
The Role of Stamping in Manufacturing
The use of stamping in manufacturing cannot be overstated. It is a cost-effective and efficient method for producing large quantities of identical parts.
The precision that stamping offers is crucial for the creation of components that meet the highest quality standards, especially in industries where even the slightest deviation can have significant consequences.
The ability to mass-produce complex parts with high accuracy makes stamping an indispensable process in the manufacturing sector.
Each step of the stamping process, from design to production, is carefully engineered to meet the highest standards. This includes using advanced computer-aided design (CAD) software for precise tooling together with high-grade materials to ensure durability and reliability.
Dedication to maintaining the highest quality control measures throughout the stamping process reflects a deep understanding of the critical role precision plays in our clients' success.
Optimisation Techniques in Stamping
Optimisation in the stamping process is vital to enhance quality and efficiency and is possible through a blend of innovative techniques and detailed execution.
One of these methods involves the use of progressive die stamping, which streamlines the production of complex parts by performing multiple operations in a single pass.
This not only speeds up the manufacturing process but also ensures uniformity and precision in each component produced. Additionally, fine blanking is a process that delivers exceptionally smooth and precise cuts, ideal for high-precision components.
Leveraging today’s technology of automation and robotics, stamping has become part of the digital revolution. New methods integrate sophisticated machinery that improves precision while reducing errors and increasing production speed.
In terms of material optimisation, it’s an issue which all responsible companies are happy to address. Again, modern methods for traditional processes can reduce waste and improves cost-effectiveness without compromising quality. These techniques, combined with rigorous quality control systems, enable the sector to set and deliver on sustainability and carbon footprint reduction.
Quality Control in Stamping
Quality control is not merely a phase in the manufacturing process; it is a vital part of the entire operation, essential for ensuring the integrity and functionality of stamped components.
Again, companies are investing heavily in the latest tech which uses laser technology to automatically check each component for safety and compliance These systems are both rigorous and robust and can spot deviations from specification on a microscopic level. These hi-tech systems ensure that each tool and die set is capable of consistently producing parts within the exact tolerances required by today’s hi-tech demands. It’s a fascinating process.
At each stage, state-of-the-art inspection equipment, including advanced coordinate measuring machines (CMMs) and vision inspection systems, are employed to conduct real-time quality checks.
This allows for immediate detection and correction of any deviation from the set standards, ensuring that every part meets the stringent criteria for precision and quality.
By systematically analysing and refining their processes, modern stamping technology not only maintains but continually elevates the standard of quality in operation.
Innovations in Stamping
Modern stamping companies are continually adopting and developing new methods and technologies. One notable innovation is the integration of advanced sensor technology in stamping presses.
These sensors provide real-time feedback on press performance. This allows for immediate adjustments to maintain accuracy and reduce downtime.
High-speed, precision stamping techniques with built in quality control can produce millions of tiny components, while operators and customers can rest assured that every last item has passed the stringent controls which are so important for the integrity of today’s hi-spec components. It's fast and 100% accurate.
Another area of innovation is in tooling design. Specialised coatings and surface treatments are used to enhance tool life and reduce maintenance requirements. Through these practices, the sector continues to flourish.
Challenges in Stamping
In the stamping industry, challenges such as material wastage, tool wear, and maintaining dimensional accuracy are widespread. Modern stamping companies address these issues with a combination of expertise, innovation, and technology. To combat material wastage, there are advanced nesting algorithms and precision tooling. Again, like magic, this new technology helps us maximise material usage and minimise scrap. It’s win win!
Maintaining dimensional accuracy, especially for complex and intricate parts, is another critical challenge. Again, rigorous quality control protocols and the use of high-precision equipment, ensure that each process delivers to the exact specifications every time.
By proactively addressing these challenges, Batten & Allen continue to deliver exceptional quality in their stamping processes.
The Future of Stamping
As the industry evolves, embracing technological advancements and shifting market demands, make the sector a very exciting place to be.
Future trends in stamping technology point towards increased automation, the integration of artificial intelligence (AI) for smarter manufacturing processes, and a greater emphasis on sustainability. It’s truly wonderful how such a traditional manufacturing method is being transformed (for the better), by the fast-moving world of technology.
Companies continue to invest in advanced automation technologies that enhance precision and efficiency, while also reducing the environmental footprint of the stamping process. There’s also the exciting potential of AI and machine learning to predict maintenance needs and optimise production schedules. So, what’s ahead? We don’t have a crystal ball but for the traditional world of stamping, maybe we should stand by for a new era of innovation.
Discover the Future of Precision Stamping with Batten & Allen
The Role of Electroplating in Precision Metal Stamping
Basics of Electroplating
Electroplating is a process that enhances the properties of metal components by coating them with a thin layer of a different metal, through an electrochemical reaction.
During this process, the parts to be plated are submerged in a solution containing the plating metal, which is then electrically charged to facilitate the transfer of metal ions onto the part's surface. This creates a bond between the two metals at a molecular level, resulting in a coating that can:
- Improve the part's resistance to corrosion.
- Increase its thickness.
- Enhance its overall strength and durability.
Benefits of Electroplating for Durability and Conductivity
Electroplating is critical in precision metal stamping for several reasons, including…
1. Increased Durability
Electroplating can significantly increase the lifespan of stamped metal parts by adding a layer of metal that resists corrosion, wear, and tear. For example, plating with nickel can create a barrier that protects the base metal from oxidising and corroding. This is particularly important in harsh environments where parts are exposed to moisture, chemicals, or extreme temperatures.
2. Enhanced Conductivity
For electrical components, conductivity is key. Electroplating with metals like gold or silver can improve a part's electrical conductivity, ensuring efficient and reliable performance in electrical applications. This is essential for components like connectors, switches, and contacts found in electronic devices.
3. Improved Solderability
Electroplating can also improve the ability of the part to be soldered, which is crucial in the electronics industry. Metals like tin are often used to plate parts to ensure a good solder joint.
4. Aesthetic Appeal
In addition to functional benefits, electroplating can also be used to improve the appearance and brightness of metal parts, which can be important for consumer-facing products.
5. Controlled Layer Thickness
Electroplating allows for precise control over the thickness of the plated layer, enabling manufacturers to ensure that parts meet exact specifications for both fit and function.
6. Selective Plating
It's possible to plate only specific areas of a component to provide conductivity or protection where it's most needed, conserving the more expensive plating material and reducing costs.
The benefits of electroplating have been pivotal in the evolution of precision metal stamping. This evolution is marked by significant technological advancements that have transformed the way metal components are manufactured.
The History & Evolution of Precision Metal Stamping
Early Methods of Metal Stamping
The history of metal stamping dates back to the early efforts of blacksmiths who used manual hammers to shape metals into desired forms. These early methods were labour-intensive and lacked the precision of modern techniques.
Over time, with the advent of the Industrial Revolution, manual labour was supplemented by steam-powered presses, which introduced the ability to mass-produce metal parts with improved consistency and efficiency.
As the demand for precision grew, especially with the rise of complex machinery and devices, so did the need for advancements in metal stamping technology. The development of mechanical presses in the late 19th and early 20th centuries allowed for the creation of more intricate parts with tighter tolerances. These machines used fixed dies and punches to shape metal sheets with each stroke of the press, a method that remains fundamental to stamping today.
Technological Advancements
The mid-20th century brought further innovation with the introduction of automated control systems, which enabled higher precision and repeatability.
The use of computers and digital technology in the latter part of the century revolutionised the field, giving rise to CNC (Computer Numerical Control) stamping machines. These machines allowed for the programming of complex and precise stamping operations, reducing the margin of error to a minimum and significantly increasing production rates.
In addition to mechanical and control upgrades, advancements in tooling materials and design have also played a crucial role. High-speed tool steels and carbide dies, for instance, have extended the life of stamping tools, allowing them to withstand the rigors of high-volume production without losing accuracy.
The transition into the 21st century has seen the incorporation of robotics, laser cutting, and 3D printing into the metal stamping process, further pushing the boundaries of what can be achieved. These technologies have enabled the production of parts with complex geometries that would have been impossible with earlier stamping methods. They also allow for rapid prototyping, which accelerates the development process and brings products to market faster.
Today, precision metal stamping is an integral component of manufacturing in a global economy, with continuous improvements in speed, precision, and versatility. Companies like Batten & Allen are at the forefront of these advancements, utilising state-of-the-art technology to meet the growing demands of industries that rely on high-quality stamped metal parts.
The Precision Metal Stamping Process
Building on the rich history and evolution of precision metal stamping, the process has become a sophisticated interplay of design, engineering, and meticulous execution.
Today's precision metal stamping process is a testament to the industry's progression, encompassing advanced design and engineering, precise tooling and die making, and a variety of stamping operations tailored to produce components with unparalleled accuracy.
Design and Engineering
The journey of a stamped metal part begins with design and engineering, where specialised software is used to create and simulate the desired part. This phase ensures that all specifications are met before any physical work begins, saving time and resources by identifying potential issues early on. Engineers consider material properties, intended use, and the complexities of design to ensure the final product will perform as required.
Tooling and Die Making
Tooling and die making are the next critical steps, where precision tools are crafted to match the part's specifications. Dies must be made with high precision to ensure that each stamped part is consistent with the original design. Batten & Allen, for instance, employs advanced tooling techniques, including modular design and wire erosion capability, to create tools that produce high-precision parts efficiently.
Stamping Operations: Blanking, Piercing, Forming, And Drawing
Stamping operations such as blanking, piercing, forming, and drawing are conducted with the tools we just discussed. Blanking cuts out the part from the metal sheet, piercing creates necessary holes or slots, forming shapes the metal into three-dimensional forms, and drawing extends the metal into complex shapes. Each of these operations requires precision machinery calibrated to exact specifications to ensure every part is a perfect replica of the last.
Quality Control and Assurance
In precision metal stamping, quality control and assurance are critical, encompassing a comprehensive regimen that begins with the scrutiny of raw materials and persists through meticulous in-process inspections and final product testing.
Utilising statistical process control to maintain consistency, and employing non-destructive testing methods for integrity verification, these practices ensure that each stamped part conforms to the exacting tolerances and finish quality required for their specific applications.
This relentless focus on quality not only fulfils the immediate specifications of customers but also feeds into a cycle of continuous improvement, enhancing the reliability and functionality of the parts in their end-use environments.
Materials in Metal Stamping
The selection of materials in metal stamping is a critical decision point that significantly affects the functionality and performance of the finished parts. Various metals are chosen based on their unique properties to match the specific demands of different applications.
Commonly Used Metals and Their Properties
Metals commonly used in stamping include steel, aluminium, copper, brass, and specialty alloys.
Steel, known for its strength and durability, is widely used in automotive and construction industries. It can be further processed into stainless steel, which offers corrosion resistance for medical and food-related applications.
Aluminium is favoured for its lightweight and corrosion-resistant characteristics, making it suitable for aerospace and consumer electronics where weight is a concern.
Copper and its alloys, like brass, are chosen for their excellent electrical conductivity and are commonly used in electrical components and connectors.
Specialty alloys may be used when a combination of properties, such as high strength, temperature resistance, or magnetic permeability, is required.
Material Selection Process
The material selection process in metal stamping involves analysing the part's required mechanical properties, environmental exposure, expected lifespan, and electrical requirements.
Manufacturers must consider the metal's formability, strength, weight, and cost-effectiveness for large-scale production. The compatibility of the metal with the intended plating process is also a crucial factor, as some metals adhere to plating better than others, influencing the durability and efficacy of the electroplating finish.
Expertise in Material Science
An understanding of material science is paramount in selecting the appropriate metal for a stamping project. Expertise in this area allows for the prediction of how different metals will behave under various manufacturing processes, including stamping and plating.
Knowledge of metallurgy helps in optimising the tool design and stamping parameters to reduce wear on the dies and increase the efficiency of the stamping process.
Manufacturers with a deep understanding of material science can provide valuable guidance during the design phase, suggesting modifications that can enhance the part's performance while keeping production costs in check. They can also help in troubleshooting issues related to material behaviour, such as unexpected brittleness or warping during the stamping process, ensuring that the final products meet the quality and performance criteria set by the client.
The Electroplating Process Explained
Electroplating involves the deposition of a metal onto a conductive surface.
The object to be plated, known as the substrate, is immersed in an electrolyte solution containing one or more metal salts. The substrate acts as the cathode of an electrical circuit, while the anode is made of the plating metal.
When an electric current is passed through the circuit, metal ions in the solution are reduced and bond to the substrate, forming a coherent metal coating. The thickness of the plating is controlled by the current and the time the substrate is left in the solution.
Types of Metal Finishes and Their Applications
Different metals are used for plating to provide various desired characteristics to the substrate. These metals include…
- Gold Plating. Used for its excellent conductivity and resistance to corrosion, ideal for high-performance electronic connectors and PCBs.
- Silver Plating. Offers superior thermal and electrical conductivity, used in areas where high-frequency performance is required, such as in satellite communications and aerospace components.
- Nickel Plating. Known for its toughness and resistance to corrosion, it is commonly applied to parts that require durability, such as in the automotive and industrial sectors.
- Chrome Plating. Provides a high gloss finish that resists tarnishing and wear, it’s often used for decorative purposes as well as functional applications like on automotive trim and plumbing fixtures.
- Tin Plating. Exhibits excellent solderability and is used to facilitate soldering in electronic components, also provides corrosion resistance and is non-toxic.
- Zinc Plating: Offers excellent rust prevention, making it a go-to for protective coatings in hardware, military, and aerospace industries.
The selection of the type of metal finish is dictated by the application's specific requirements, including environmental exposure, electrical demands, wear conditions, and aesthetic preferences.
Each finish not only extends the functionality and service life of the component but can also contribute to its visual appeal. The process of choosing the right electroplating finish is a careful balance between performance specifications and cost-efficiency.
Batten & Allen's Electroplating Capabilities
Batten & Allen's robust electroplating capabilities are a testament to their dedication to delivering comprehensive in-house solutions.
Their state-of-the-art facility is equipped with eight specialised electroplating lines, including a £1.25 million investment in advanced reel-to-reel technology. This setup not only underscores their commitment to maintaining control over the electroplating process but also demonstrates their ability to provide high-quality, consistent finishes across a vast production scale.
With the capacity to pre-plate continuous coil material and plate stamped components reel to reel, they ensure efficiency and precision in every run.
In-House Electroplating Facilities
The in-house electroplating facilities at Batten & Allen represent a significant stride towards maximum self-sufficiency.
By designing and constructing their own high-speed plating lines, they have set themselves apart in the ability to rapidly produce and iterate high-quality plating for various components.
Their engineers' direct involvement in the plating process, supported by a fully equipped process laboratory, allows for meticulous control over the plating solutions and thickness, aligning with both customer specifications and environmental regulations.
Customisation Options for Various Industries
Batten & Allen's expertise in material science shines in their customisation options, which cater to the nuanced needs of diverse industries. They offer a spectrum of electroplating services tailored for electronics, automotive, medical, and industrial applications, ensuring that each sector receives components manufactured to exact standards.
Their ability to produce multi-impression fine-tolerance lead frames, connectors, and other precision parts with pre-plated, post-plated, or selective plating options allows them to serve market sectors with high efficiency and low unit costs, providing a complete solution from design to final product.
Quality and Compliance in Electroplating and Metal Stamping
In the electroplating and metal stamping industry, adherence to quality and compliance standards is paramount to ensure the production of safe, reliable, and superior-quality products.
Manufacturers across the sector are governed by a complex set of international standards, including ISO 9001 for quality management systems, ISO 14001 for environmental management, and ISO/TS 16949 for the automotive sector, which specify requirements for consistent product quality and regulatory compliance.
Industry Standards for Electroplating and Metal Stamping
The industry standards, such as those set by the International Organization for Standardization (ISO), provide a framework for best practices in manufacturing. These standards help companies establish a systematic approach to managing their processes and are critical for ensuring product quality.
For instance, ISO 9001 certification is a widely recognised standard that demands a quality management system to guide and control manufacturing operations effectively. This certification requires manufacturers to undergo rigorous evaluation processes to demonstrate their commitment to product quality, customer satisfaction, and continuous improvement.
Environmental Considerations and Sustainability
Environmental sustainability is a significant concern in the metal stamping and electroplating industry. Standards like ISO 14001 encourage organisations to minimise harmful effects on the environment caused by their activities and to achieve continual improvement of their environmental performance. This involves careful management of chemical use in electroplating, efficient waste management, and the adoption of recycling practices.
By following these guidelines, manufacturers contribute to a more sustainable manufacturing cycle and demonstrate corporate responsibility. Compliance with such environmental standards is not only ethically important but also serves to enhance the marketability of products in an eco-conscious consumer market.
Transitioning from the focus on environmental considerations and sustainability, it's important to recognise how these principles are applied in specific industries. The electronics industry, in particular, stands out as a significant area where precision metal stamping and electroplating play crucial roles.
Connectors and Semiconductor Components
In the realm of electronics, connectors and semiconductor components are critical for ensuring the efficient and reliable operation of electronic devices. Connectors, which facilitate electrical connections between different parts of a device, require precise manufacturing to ensure consistent performance.
Similarly, semiconductor components, which form the backbone of electronic circuits, demand high precision in their construction. Metal stamping and electroplating play vital roles in creating these components, offering the precision, durability, and conductivity needed for the electronics industry.
Away from the specifics of the electronics industry, it becomes evident that the expertise in precision metal stamping and electroplating extends far beyond just one sector. The versatility of these manufacturing techniques is showcased in their application across a diverse range of industries, each with its unique requirements and challenges.
Beyond Electronics: Diverse Applications
While the electronics industry significantly benefits from precision metal stamping and electroplating, these manufacturing techniques are equally vital across a variety of other sectors. Their adaptability allows for customisation to meet the specific needs of different industries, highlighting the broad impact and importance of precision metal stamping and electroplating in modern manufacturing.
Automotive, Aerospace, and Telecommunications Sectors
In the automotive industry, precision metal stamping and electroplating are indispensable for producing a range of durable and reliable components. These include connectors, sensors, and various engine parts, all of which are essential for the functionality and safety of vehicles.
The aerospace sector, known for its stringent quality and safety standards, relies heavily on these processes. Precision metal stamping and electroplating are used to create critical components for aircraft and spacecraft, where the highest levels of precision and strength are required. These components often include structural elements, engine parts, and electrical systems, all of which must withstand extreme conditions and stresses.
In the telecommunications sector, precision metal stamping and electroplating play a crucial role in manufacturing components for communication devices and infrastructure. This includes components for mobile devices, satellite communications, and network hardware. The precision and conductivity achieved through these processes are essential for ensuring reliable and high-speed communication, which is the backbone of the modern digital world.
Each of these sectors demonstrates the versatility and necessity of precision metal stamping and electroplating in creating components that meet the highest standards of quality, durability, and performance.
Custom Solutions for SMEs Across Various Sectors
Small and medium-sized enterprises (SMEs) across various sectors also benefit from the custom solutions provided by precision metal stamping and electroplating services.
These manufacturing techniques offer SMEs the flexibility to produce specialist components tailored to their specific needs, whether it's for niche markets or innovative new products.
By providing access to high-quality, custom-manufactured components, precision metal stamping and electroplating play a pivotal role in supporting the growth and diversification of SMEs in a wealth of industries.
Moving from the discussion on custom solutions for SMEs, it's crucial to delve into the collaborative aspect of manufacturing, particularly in the realm of design engineering. This collaboration is key to developing effective, innovative solutions that meet the specific needs of diverse industries.
Design Engineering and Collaboration
The intersection of design engineering and manufacturing is a dynamic space where creativity meets practicality. In this realm, the collaboration between design engineers and manufacturers is essential for translating innovative concepts into tangible, functional products.
This partnership is especially critical in industries where precision and customisation are paramount, as it ensures that the final products not only meet but exceed the expectations and requirements of the end-users.
Partnering with Design Engineers
Partnering with design engineers involves a synergistic relationship where the expertise of both parties is leveraged to achieve optimal outcomes.
Manufacturers bring their practical knowledge of materials, processes, and production constraints, while design engineers contribute their vision, innovation, and technical design skills. This partnership is crucial in navigating the challenges of product development, from conceptualisation to final production, ensuring that each step of the process is aligned with the project's goals and specifications.
Co-Development Processes
Co-development processes represent the epitome of this collaborative effort, where manufacturers and design engineers work hand-in-hand throughout the product development lifecycle.
This approach allows for continuous feedback and iteration, ensuring that the design is feasible from a manufacturing perspective and that the manufacturing process is tailored to realise the design effectively.
Co-development fosters a deeper understanding of the project's objectives and challenges, leading to more innovative solutions, efficient production, and ultimately, higher-quality products. This collaborative approach is particularly beneficial in sectors where cutting-edge innovation and precision are crucial, such as in advanced electronics, medical devices, and aerospace engineering.
Transitioning from the co-development processes, where design engineers and manufacturers collaborate closely, the journey of bringing a product from concept to reality involves several critical stages. This journey is characterised by meticulous prototyping, rigorous testing, and the eventual scaling of production, all while maintaining the highest standards of precision and quality.
From Concept to Reality
The transformation of a concept into a tangible product is a complex and multifaceted process. It begins with an idea or a design, which then undergoes various stages of development and refinement.
This journey is not just about the creation of a physical product but also about ensuring that the product meets all the functional, aesthetic, and quality requirements set forth at the concept stage.
Prototyping and Testing
Prototyping is an essential step in the product development process. It involves creating a preliminary model of the product to test its feasibility, functionality, and design. This stage allows manufacturers and designers to identify potential issues and make necessary adjustments before full-scale production.
Testing, both during and after the prototyping phase, is crucial to validate the product's performance under various conditions and to ensure it meets all safety, quality, and regulatory standards. Rigorous testing helps in fine-tuning the product, ensuring that it is ready for the market.
Explore the world of precision metal stamping with Batten & Allen: Mastering Metal Stamping
Getting Started with Batten & Allen
Whether you're looking for a long-term partnership or need assistance with a specific project, Batten & Allen's approachable and professional team is ready to guide you through the process.
Contact us now!